Rebuilding / Recelling a Cordless Drill Battery
|
|
Here is a short description of how I opened a DeWalt cordless drill
XR battery and replaced the cells inside. Why? I'm curious. I like to
see how stuff goes together. I like fixing things in this disposable
age. Read on for tales of electrical shorts, smoke, and cadmium.
PLEASE NOTE!
- This information is provided only to show you how I did this.
- This is not intended to encourage any such behavior on your part.
- Any repair or modification to these things can be dangerous:
- Miswired cells can explode or catch fire;
- Cadmium is deadly to humans and pets;
- Solder may contain lead;
- Something could go so seriously wrong that causes a tragic domino
effect destroying your city, state, country, and civilization as we
know it, reducing the planet to a desolate charred landscape with only
the occasional one-winged smoldering cockroach plying the ruins.
- Not to mention - you will certainly void your warranty.
- Don't even try this. Go away.
(That said, read on to
hear what I did!)
Some safety precautions I observed while doing this:
- Washing hands after touching NiCad's. Cadmium is
nasty.
- Always treating the cells as if they were charged.
- Never allowing any wire, cell tabs, or metal to touch another.
- Triple taping areas where the sharp edges of the soldering tabs
could cut through the tape
Parts list:
- Sub-C replacement cells: "high discharge" high capacity (2500mAh) 1.2V
with soldering tabs
(These were found with a simple web search.
I used NiCads: the originals were, the charger was made for them,
and the only "high discharge" cells I could find were NiCads.)
- High-temperature 18ga. wire
(The original wire inside the case was 16 ga, but I found this
too hard to deal with. The 18 has
handled the high discharge amperage without overheating.)
- High-temperature electrical tape
- High-temperature duck tape
- Soldering iron, solder
Cost breakdown: (10) $1.95 cells = $19.
Cost of a new OEM battery: $45.
Total time: 2hrs.
That comes down to $13/hour for my time. [Update: +1/2 hour spent
repairing a short where the sharp edge of a solder tab cut through the
electrical tape. Smoke. Flame. Now at $10.40/hour.]
See - it's not worth it. Don't
try this. Play with your kids instead - maybe they won't turn out as career
criminals after all.
|
|
Opening the battery case
- I used a dremel tool with a spiral bit to carefully cut open
the bottom of the battery case about 1/16'' above the bottom, being very
careful to not cut through into a battery. Think cadmium.(fig 1,2)
- I pulled off the bottom of the case, and slid the battery pack
out.(fig 3,4)
- I cut open the plastic wrap around the cells with ordinary
scissors and unwrapped the cells. Note that the contacts for the whole
battery pack are attached to the topmost cell, which lies inside the
upper body of the pack.(fig 5,6)
|
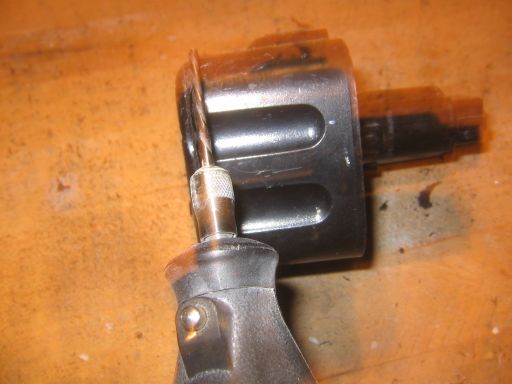
fig 1
|
|
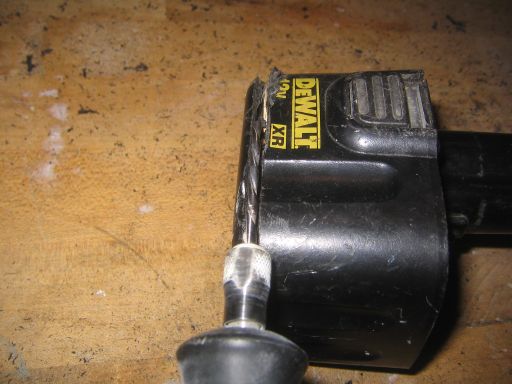
fig 2
|
|
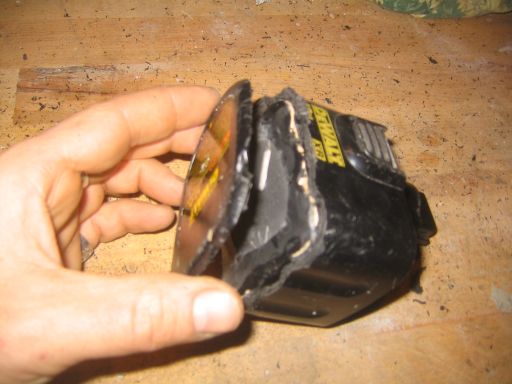
fig 3
|
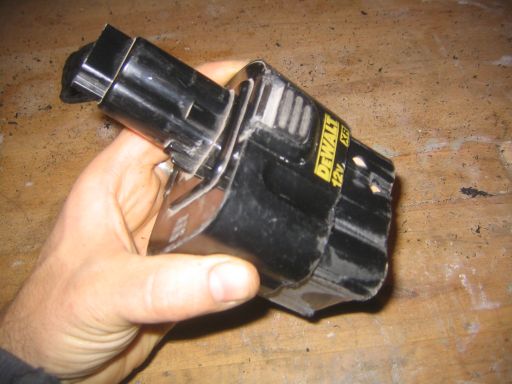
fig 4
|
|
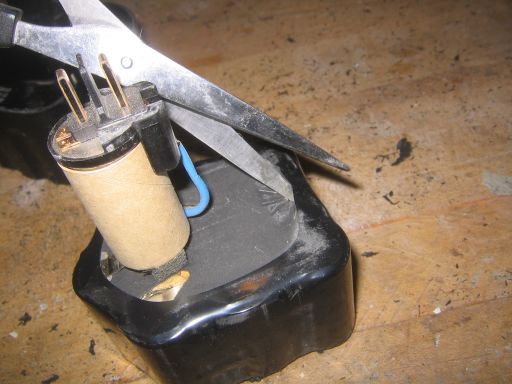
fig 5
|
|
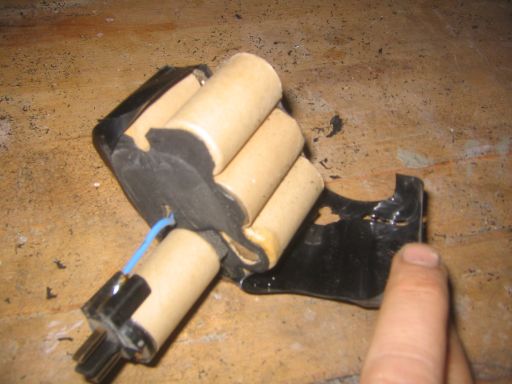
fig 6
|
|
Separating the cells and the parts
- Peeling off a thin layer of tape on the bottom of the cells
revealed solder tabs connecting the batteries together.(fig 7)
- I cut the solder tab holding the topmost cell onto the
lower pack of cells.(fig 8)
- I slid the cardboard sleeve off the cell, and removed the plastic
ring underneath.(fig 9,10)
- I used a razor knife to carefully cut the solder tab holding the
battery contacts to the top of this cell. The battery contacts will be
reused for the new pack.(fig 11,12)
|
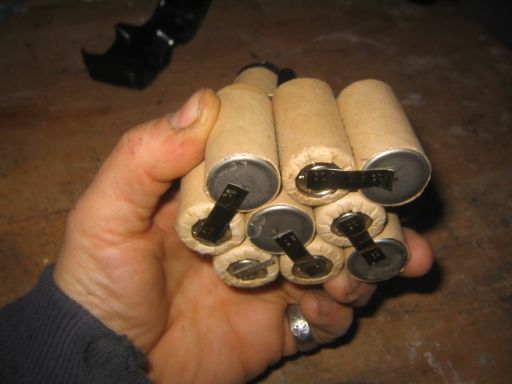
fig 7
|
|
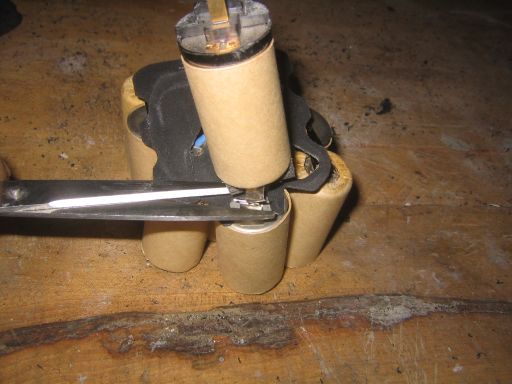
fig 8
|
|
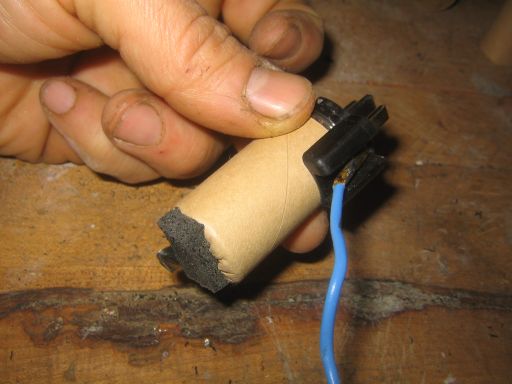
fig 9
|
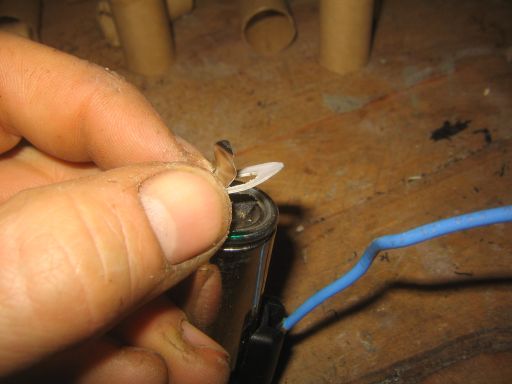
fig 10
|
|
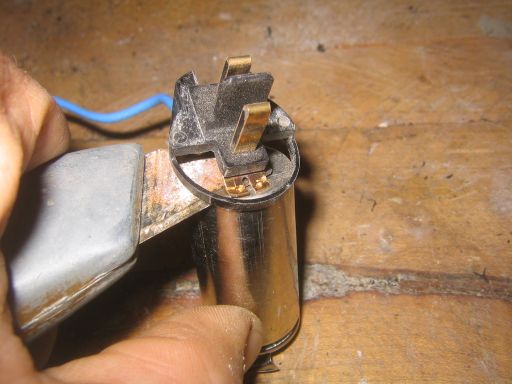
fig 11
|
|
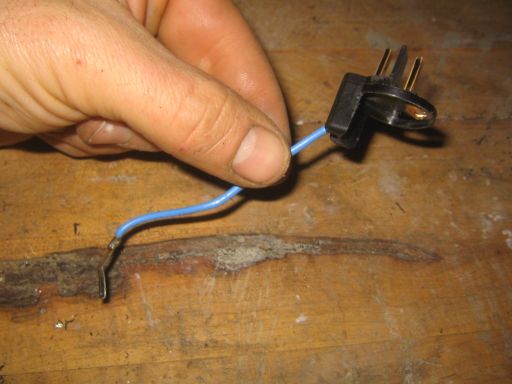
fig 12
|
|
Soldering the new cells
- REMEMBER: the cells have charge in them right from the
box. As they are connected together, the resulting voltage will increase,
as will the shock and fire hazard if accidentally shorted!
- Here's a comparison of the old and the new
cells.(fig 13,14)
- I cut a bunch of 1.5'' pieces of wire, and stripped 1/4'' from
each end.(fig 15)
- I punched a hole into each solder tab with an
awl.(fig 16)
- I threaded a wire through the hole,(fig 17)
- And soldered it onto the tab.(fig 18)
- 9 of the cells were laid out in the same pattern as the old
cells, noting both the overall pattern and which were (+) or (-) side
up, in order to see which tabs to solder. The cells are all soldered
in series, meaning that (+) poles are soldered to (-) ones. The 10th cell
will be soldered to the top of this pack.(fig 19)
- Connected cells are soldered together, and any exposed solder
tab ends are wrapped with high temperature electrical
tape. (This could be done better by bending and soldering adjacent tabs
together directly, and using heat-shrink tubing
everywhere....)(fig 20,21)
- The wire and the solder tab on the plastic piece with the
battery pack contacts are lengthened with wire.(fig 22)
- The correct pole of the 10th battery is soldered onto the
inner wire of the contacts.(fig 23)
- The solder tab for the other pole of the 10th battery is
soldered directly to the solder tab of the middle front battery of the
pack of 9, so that it will sit low on top of the main pack.(fig 24)
- All of the soldered connections are protected with heat shrink
tubing.(fig 25)
- Here is my completed battery pack with only the last wire of the
contacts left to connect.(fig 26)
- I tested the voltage with a multimeter, to ensure all the
cells were correctly connected.(fig 27)
|
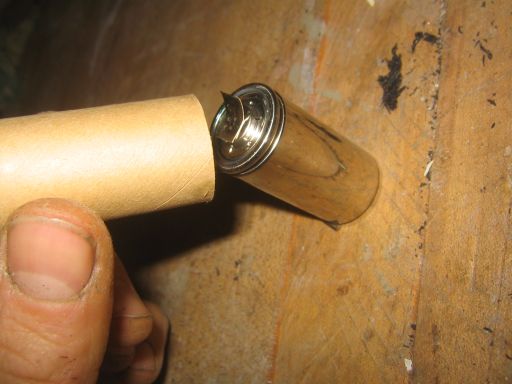
fig 13
|
|
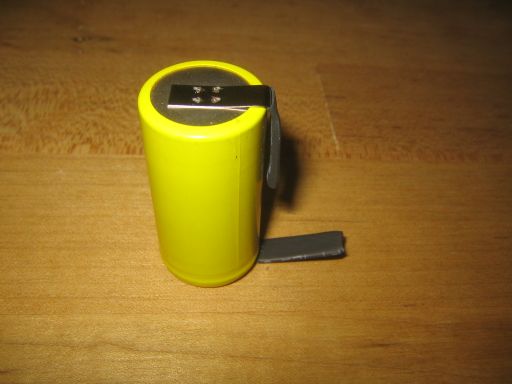
fig 14
|
|
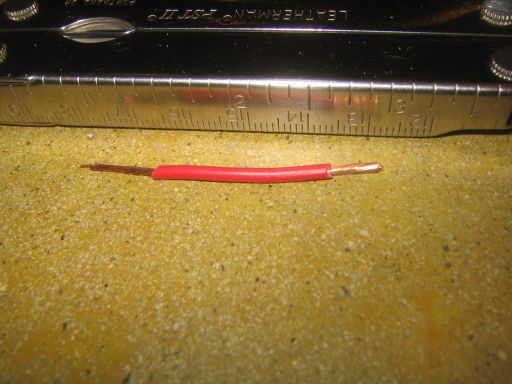
fig 15
|
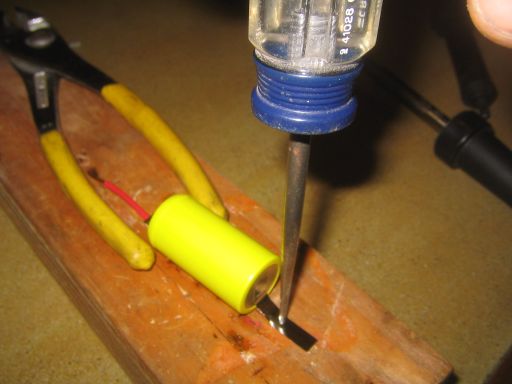
fig 16
|
|
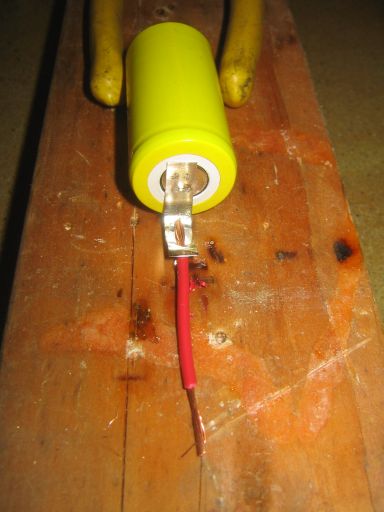
fig 17
|
|
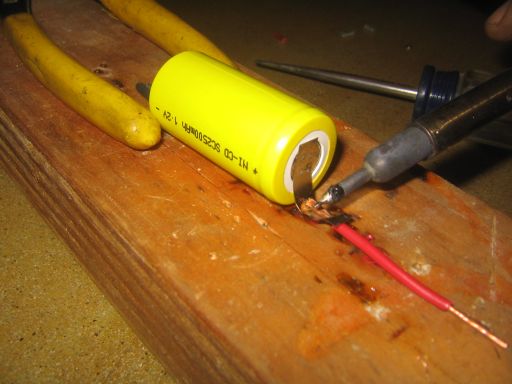
fig 18
|
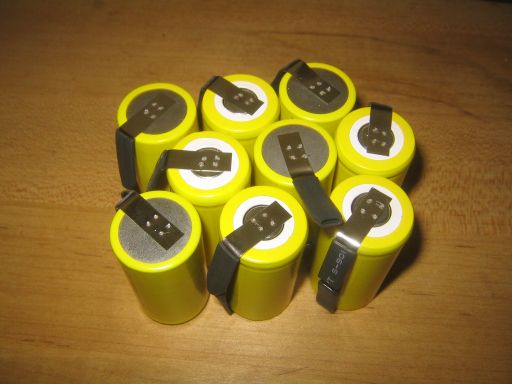
fig 19
|
|

fig 20
|
|
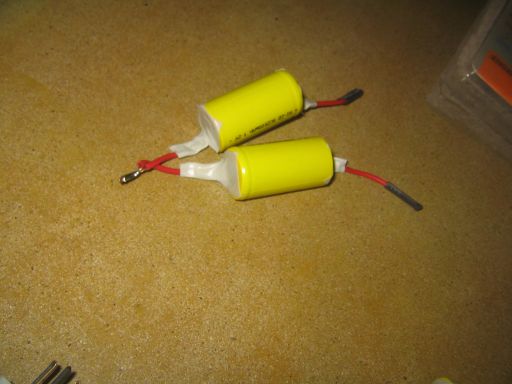
fig 21
|
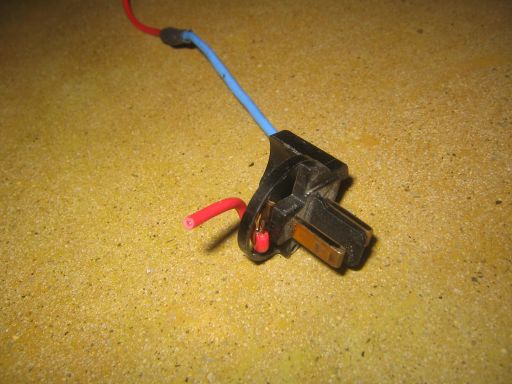
fig 22
|
|
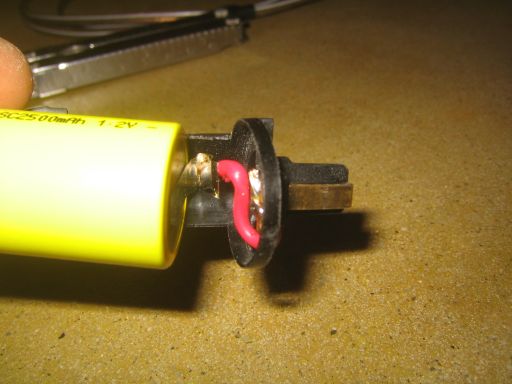
fig 23
|
|
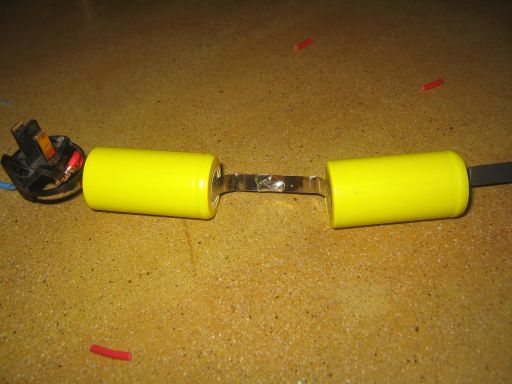
fig 24
|
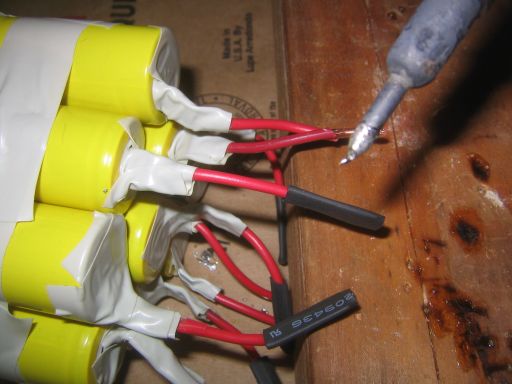
fig 25
|
|
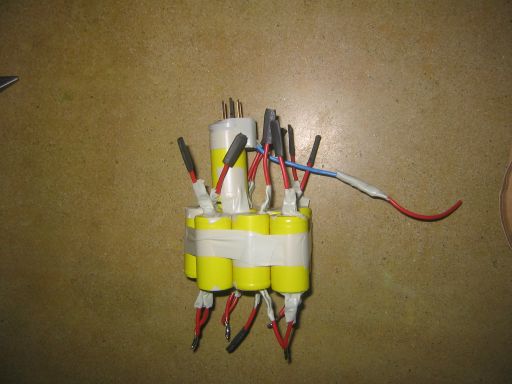
fig 26
|
|
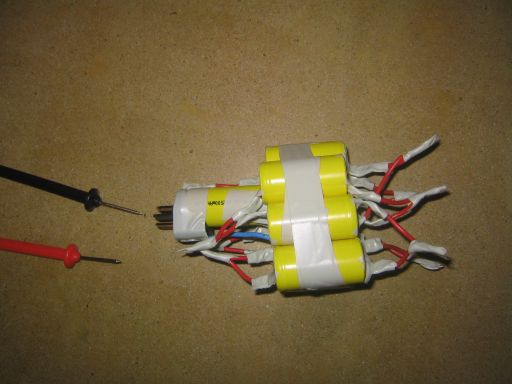
fig 27
|
|
Reassembling the battery pack
- The cell pack was carefully inspected for any exposed contacts
or wire, and taped several layers thick between edges and under the
topmost battery. The pack was slid into the old casing, ensuring
the contacts ended up in the correct place.(fig 28,29)
- Good ole duck tape was used to hold the old bottom of the
case on...great, but jenking it together like this makes the structural
integrity of the whole pack suspect.(fig 30)
- The work was inspected by the local
inspector.(fig 31)
- REMEMBER: something like this must be tested carefully,
and SHOULD NOT BE LEFT UNATTENDED WHEN CHARGING FOR THE FIRST FEW
TIMES!! I watched carefully as the pack was charged, placing the
charger on a non combustible surface. No problems here.
-
HOWEVER, I did have a short on the first test -
I tested the pack at high load (causing high current
discharge in the pack).
A short caused smoke and melted plastic where the
sharp edge of one of the solder tabs cut through insulation!! The short
was easily fixed, but could have caused serious damage if it happened
some time later.
-
That said, my re-celled battery pack has lasted 5 years
and counting!
|
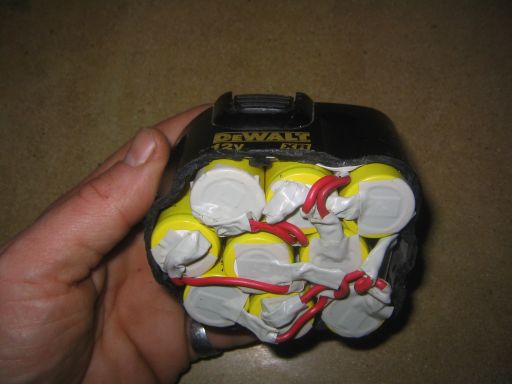
fig 28
|
|
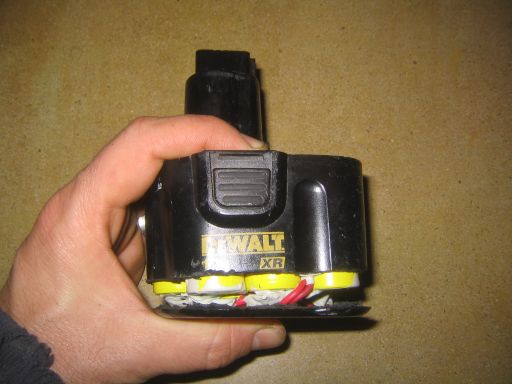
fig 29
|
|
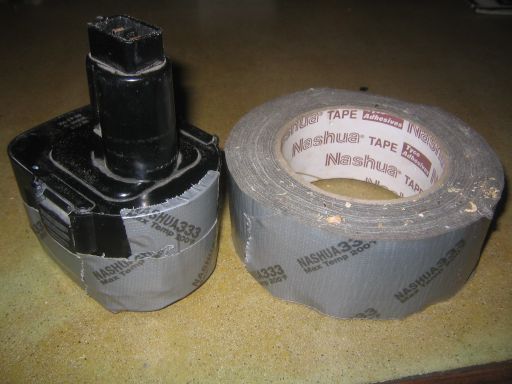
fig 30
|
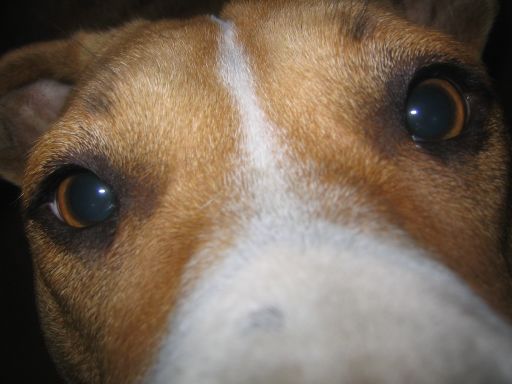
fig 31
|
|
|
|
|
|